


.jpg)

 |
Tischmesserschmied 2 |
"Alle Handwerke der Schmiede, der Herder und Schleiffer,
der Feger, der Metzmacher sind zugleich uff das Metzmachen privilegiert
und mögen ohne Unterschied sich des Metzmachens gebrauchen." so
niedergeschrieben 1619 um zu begründen, dass der Beruf "freigegeben"
werden sollte für alle Solinger Handwerker, da das Schwertschmieden
alleine nicht ausreichen konnte, die Menge der seinerzeit schon
vorhandenen Handwerker zu nähren. So gesehen ist die Basis des Solinger
Weltruhms, die Qualität der Tischmesser, eher Not denn Tugend.
|
Hier in der schematischen Zeichnung sind Amboss und
Prahm (zum Opdriwen, siehe oben) noch besser zu erkennen.
Her Huwescher, diese Zange mit dem besonders langen
Hebel, diente zum Abschneiden der geschmiedeten Klinge auf die Länge des
jeweiligen Modells, das hergestellt wurde und für das Abrunden des
vorderen Teils der Schneide; im Grunde genommen handelt es sich beim
Huwescher um eine besonders kräfte "Blechschere", eben eine für Eisen.
Das Zudrücken geschah, indem der lange Hebel unter dem rechten Arm
gedrückt wurde und das zu bearbeitendes Stück so geschickt zu halten war,
dass die Schnitte es nicht unbrauchbar machten.
Die Schärfte, den Schliff, brachten dann die
Messerschleifer in weiteren Arbeitsgängen an. Anschließend wurden die
Klingen poliert, gepliestet (blaugepliest). |
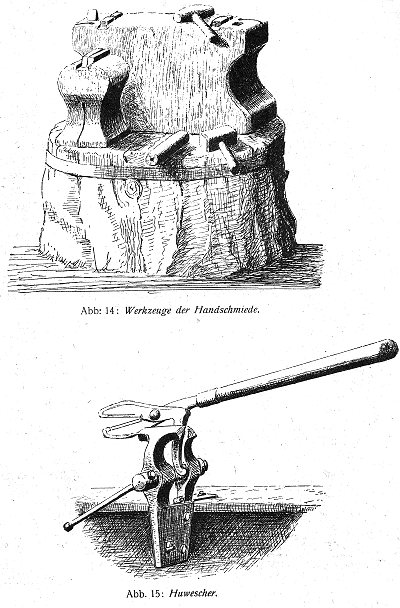 |
Ein Schmied galt um 1850 als tüchtig, wenn er
täglich um die 50 Tischmesserklingen herstellte. Das aber setzte voraus,
dass am gesamten Arbeitstag nichts schief ging, kein einziger
Arbeitsschlag daneben war. Die alten Schleifer erzählen, dass es der
Rhythmus der Arbeit war, der diese Leistung ermöglichte. Nicht zu
schnell, nicht zu langsam. Und dieser Rhythmus, so geht die Sage, sei
irgendwie im Bergischen "fühlbar" gewesen. Es gibt ernsthafte
Schilderungen, die davon berichten, dass ausgewanderte Solinger Schmiede
in der Fremde bei den gleichen Arbeiten und mit gleichem Werkzeug nicht
mehr den Rhythmus gefunden und damit die Leistung nicht mehr ereicht
haben. Dem Widerhall aus letztendlich hunderten von Werkstätten im
Stadtgebiet von und um Solingen verdankt dieser Teil des Bergischen
übrigens das Attribut der "singenden, klingenden Berge": Es sind sind
Lieder schmetternde Menschen, die diesen poetischen Begriff assoziierte,
sondern der Rhythmus der Schmiedehämmer! |
Dem legendären und sagenumwobenen schwäbischen
Tüftler steht der Solinger "Prakesierer", Denker und Erfinder, in nichts
nach. Die gesamte fertigungstechnische Entwicklung, ein Teil des immer
härter werdenden Wettbewerbs basiert auf tausenden von kleinen oder
epochalen Verbesserungen der Arbeitsvorgänge und damit der
Geschwindigkeit und Qualität; beides zusammengefasst in einer neuen
Wirtschaftlichkeit oder dem Überleben im Konkurrenzkampf. |
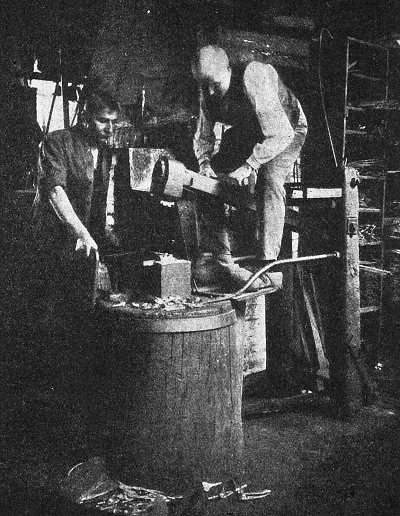 |
Um die Wucht des Hammers zu erhöhen (ohne
Wasserkraft), wurde dieser Bockhammer erfunden. Auf dem "Bock" (einem
Sitzgestellt) sitzend hebt der Schmied an einem Quergriff den Hammer, der
zwischen zwei senkrechten Pfählen auf einem Hebel fixiert ist und lässt
ihn schlagartig fallen - der erste Fallhammer also !
So erfunden um 1848; es ist der Anfang des später
verbreiteten, hochproduktiven Gesenkschmiedens. Dabei wird das Messer
wird auf einen Schlag in einer Form gefertigt, dem Gesenk. Und dazu
benutzt man so genannte Fallhämmer mit einem schweren Kopf (dem Bär), die
von Riemen über erst mit Dampfkraft, später mit Strommotoren bewegte
Scheiben hochgezogen wurden.
|
Noch einen Schritt weiter ging der Federhammer,
eine Eigenerfindung in der Schmiede der Hartkopfs. Die Federn (sie
herzustellen bedurfte es damals extremer Anstrengungen) fingen einen Teil
der Rückschlagskraft wieder auf, so dass mittels es Hebels der Schmied
tatsächlich nur die verbrauchte Energie (Kraft) per Fußtritt auf einen
Hebel wieder zuführen musste. Hätte man seinerzeit schon die
Begriffe gekannt, die Idee wäre für eine Supersonder-Auszeichnung in
"praktischer Ökologie" und "resourcen-schonendem Workflow-Reengineering"
gut gewesen. |
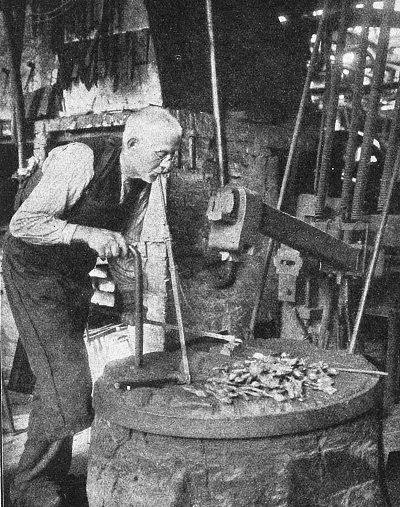 |
|
Geräumig waren die Werkstätten nicht gerade. Heiß
und laut war es auch. Und es stank, denn sowohl Kohle wie auch der
geschmiedete Stahl, öfter auch in Flüssigkeiten getaucht, geben Dämpfe
ab. Vielleicht aber war es auch in einer gewissen Art und Weise
"gemütlich", weil überschaubar - und eine Werkstatt, die man sich nach
eigenem Ermessen zusammengestellt hatte.
Diese Schmiede, im Grundriss wiedergegeben, wurde
als Erweiterungsbau der ursprünglichen Schmiede (siehe Zeichnung zu
Anfang) in einer Scheune errichtet, als "Unternehmens-Expansion".
Später, um 1883, zog das Unternehmen näher an
Solingen heran, auf die Dorper Rathausstraße. Hier war bis dato eine
Windmühle zum Zerkleinern von Schmirgel in Betrieb gewesen. 1887 erfolgte
die Eintragung im Handelsregister unter "Gebrüder Hartkopf". Das
Unternehmen ist heute in Solingen mit Adresse auf der Bismarckstraße zu
finden.
1909 erfolgte ein Aufspaltung des Unternehmens, der
neue / andere Teil firmierte unter Carl August Hartkopf, das
Fabrikgebäude war auf der Ritterstraße (ebenfalls Dorp).


 |
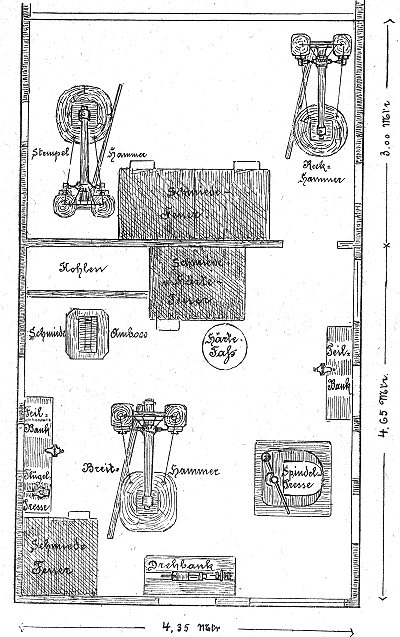
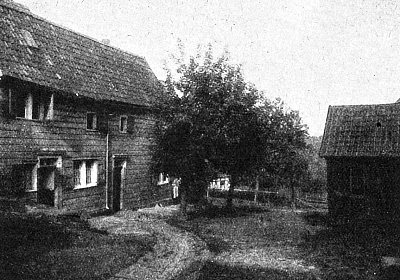
|
|
Erstaunlich, schon damals konnten es die Solinger
einfach nicht lassen, sich in hunderten von Modellen und Mustern zu
ergehen. Natürlich werden die Fachleute einwenden, dass jedes einzelne
Modell der Messer seine besondere Berechtigung für spezielle Benutzungen
hat; dagegen ist nichts einzuwenden. Allein, es macht die Produktion
nicht kostengünstiger. |
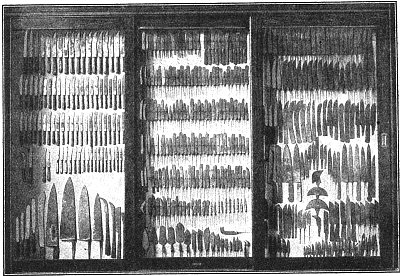
|
|
In späteren Jahren wurde das Unternehmen immer mehr
von der Schmiede zur Fabrik mit Massenproduktion; Halbautomaten,
Zweischlag- und Vierschlaghämmer, Spalt- und Asstanzpressen erleichterten
einerseits die Arbeit, waren aber andererseits auch notwendig, um dem
globalen Wettbewerb und dem Qualitätsniveau der Solinger
Messermacher-Industrie standzuhalten.
Die Arbeitsbedingungen in dieser industriellen
Fertigung waren nicht unbedingt optimal, aber seinerzeit galt es noch als
völlig normal, dass sich der Mensch der Maschine anzupassen hat;
"Ergonomie" und "Arbeitsschutz" waren unbekannte, weil noch nicht
erfundene oder benutzte Worte. |
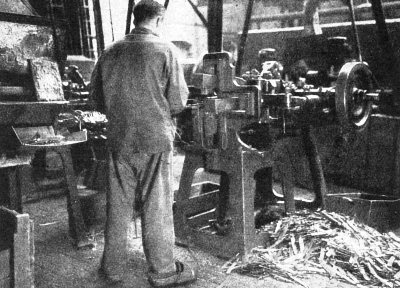
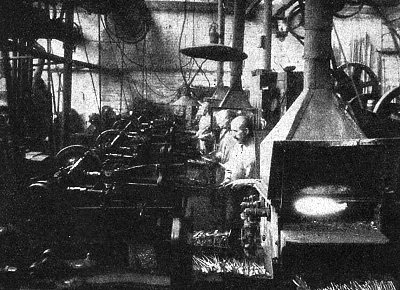 |
|
|
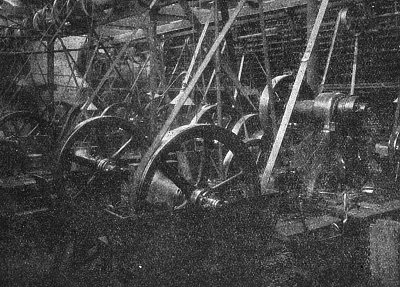 |
|
Aus den Bockhämmern wurden irgendwann Fallhämmer,
alles größer, alles schneller, alles rationeller. Und diese wuchtigen
Hämmer eigneten sich dann auch für viele andere Teile, nicht nur Messer,
so dass das Unternehmen Gebr. Hartkopf ein breites Produktspektrum
anbieten konnte und dies heute noch tut. |
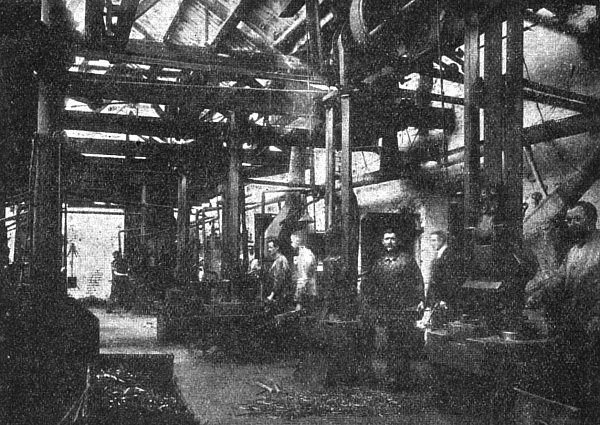
|
Zwei der Messerschmiede-Pioniere auf der Grenze von
zünftigem Handwerk und industrieller, kaufmännisch gelenkter
Massenproduktion: Carl Hartkopf sen (gestorben 1919) und August Hartkopf,
der zum Erscheinen des Buches 1922 als Pensionär sich der Garten- und
Obstpflege widmete. |
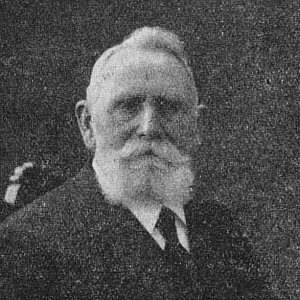 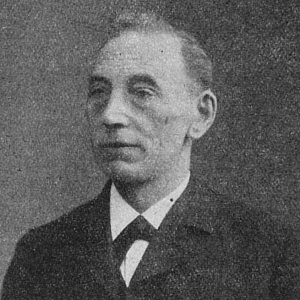
|
|
|
|
|
|
|
.jpg) |
|
|